What is Porosity in Welding: Important Tips for Achieving Flawless Welds
What is Porosity in Welding: Important Tips for Achieving Flawless Welds
Blog Article
The Science Behind Porosity: A Comprehensive Guide for Welders and Fabricators
Recognizing the elaborate systems behind porosity in welding is important for welders and fabricators aiming for impressive workmanship. From the structure of the base materials to the ins and outs of the welding procedure itself, a plethora of variables conspire to either exacerbate or minimize the existence of porosity.
Understanding Porosity in Welding
FIRST SENTENCE:
Examination of porosity in welding discloses critical understandings into the stability and high quality of the weld joint. Porosity, identified by the presence of tooth cavities or spaces within the weld metal, is an usual problem in welding procedures. These gaps, if not effectively resolved, can compromise the structural stability and mechanical residential properties of the weld, leading to potential failings in the completed item.

To find and quantify porosity, non-destructive testing techniques such as ultrasonic screening or X-ray evaluation are commonly used. These methods enable for the recognition of interior issues without compromising the honesty of the weld. By examining the dimension, shape, and circulation of porosity within a weld, welders can make informed choices to boost their welding processes and attain sounder weld joints.
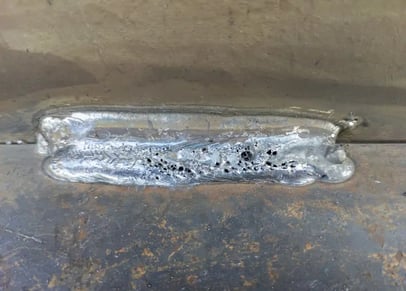
Factors Affecting Porosity Formation
The occurrence of porosity in welding is influenced by a myriad of factors, varying from gas shielding efficiency to the complexities of welding criterion setups. One critical aspect adding to porosity development is inadequate gas shielding. When the securing gas, commonly argon or CO2, is not properly covering the weld swimming pool, climatic gases like oxygen and nitrogen can infect the molten metal, causing porosity. In addition, the tidiness of the base materials plays a considerable role. Impurities such as corrosion, oil, or wetness can evaporate throughout welding, producing gas pockets within the weld. Welding parameters, consisting of voltage, present, take a trip speed, and electrode kind, also impact porosity development. Making use of improper setups can produce too much spatter or warmth input, which consequently can news result in porosity. The welding strategy employed, such as gas metal arc welding (GMAW) or shielded steel arc welding (SMAW), can affect porosity formation due to variants in heat circulation and gas insurance coverage. Understanding and managing these factors are necessary for minimizing porosity in welding procedures.
Effects of Porosity on Weld Top Quality
Porosity formation dramatically endangers the structural integrity and mechanical homes of welded joints. When porosity exists in a weld, it produces gaps or tooth cavities within the material, lowering the general toughness of the joint. These spaces function as tension concentration points, making the weld much more susceptible to breaking and failing under load. The presence of porosity additionally damages the weld's resistance site web to deterioration, as the entraped air or gases within deep spaces can react with the surrounding environment, leading to destruction with time. Furthermore, porosity can prevent the weld's capacity to withstand pressure or influence, more jeopardizing the general high quality and dependability of the bonded structure. In vital applications such as aerospace, automobile, or structural constructions, where safety and resilience are critical, the destructive impacts of porosity on weld top quality can have serious effects, stressing the relevance of decreasing porosity with correct welding methods and treatments.
Strategies to Minimize Porosity
Additionally, utilizing the suitable welding specifications, such as the right voltage, current, and take a trip rate, is crucial in avoiding porosity. Preserving a regular arc size and angle throughout welding also helps decrease the probability of porosity.

Making use of the ideal welding method, such as back-stepping or utilizing a weaving motion, can additionally assist distribute warmth uniformly and reduce the chances of porosity development. By carrying out these methods, welders can effectively decrease porosity and create top quality welded joints.
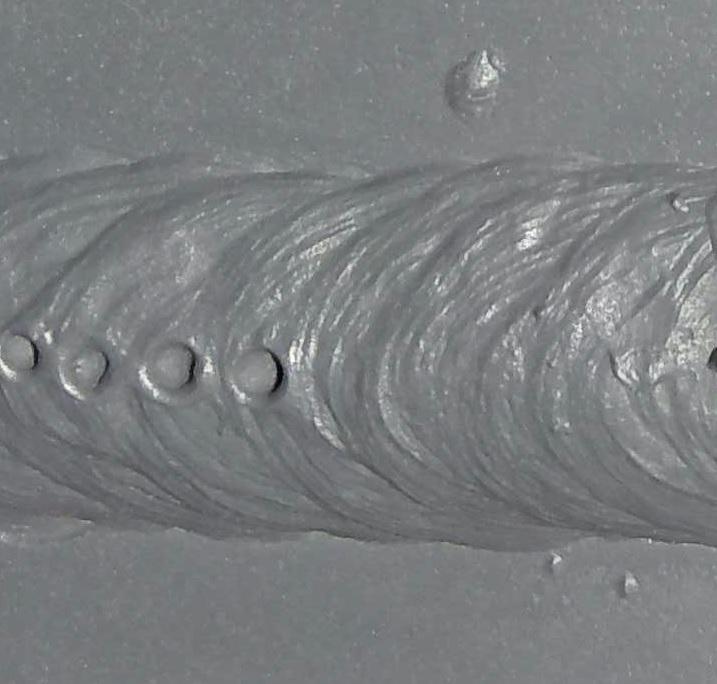
Advanced Solutions for Porosity Control
Implementing sophisticated innovations and ingenious methods Related Site plays a crucial function in attaining exceptional control over porosity in welding procedures. Additionally, utilizing advanced welding methods such as pulsed MIG welding or modified environment welding can also assist minimize porosity concerns.
One more innovative service includes using sophisticated welding tools. Using equipment with integrated functions like waveform control and sophisticated power sources can improve weld high quality and decrease porosity threats. Moreover, the execution of automated welding systems with exact control over specifications can considerably minimize porosity defects.
Additionally, integrating innovative tracking and assessment technologies such as real-time X-ray imaging or automated ultrasonic screening can help in detecting porosity early in the welding procedure, permitting instant restorative actions. In general, incorporating these innovative remedies can greatly improve porosity control and boost the general high quality of bonded elements.
Final Thought
In conclusion, understanding the science behind porosity in welding is necessary for welders and producers to produce premium welds. By identifying the elements influencing porosity formation and carrying out techniques to lessen it, welders can improve the total weld quality. Advanced options for porosity control can even more boost the welding procedure and ensure a strong and reputable weld. It is very important for welders to continually inform themselves on porosity and carry out finest practices to achieve optimum results.
Report this page